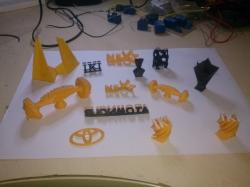
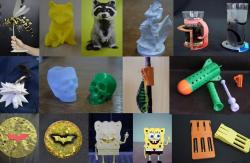
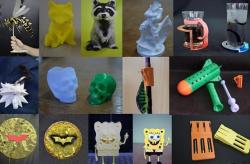
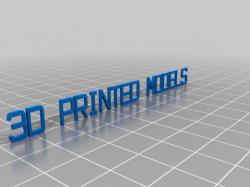
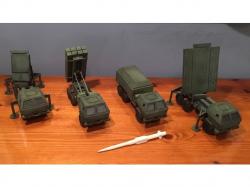
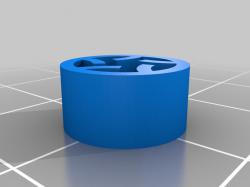
Understanding 3D Printed Bearings
Bearings play a pivotal role in a wide range of machines, facilitating the smooth operation of moving parts. Traditional bearings are typically made from robust materials like steel, but with 3D printing, it’s possible to create bearings from plastics like PLA (Polylactic Acid). While 3D printed bearings might not match the strength and durability of their metal counterparts, they offer significant advantages in terms of customization and rapid prototyping.
Designing 3D Printed Bearings
The design process of 3D printed bearings is crucial for their functionality. Unlike traditional bearings, which require precise calculations and manufacturing techniques, the design of 3D printed bearings can be more flexible. However, it’s essential to consider factors like the size of the air gap between rolling elements and the casing, the number of rolling elements, and the dimensions of the bearing. For instance, a typical design might have an inner diameter of 10 mm, an outer diameter of 30 mm, and around 11 or 12 rollers.
Printing Techniques for Bearings
When it comes to printing bearings, several factors need consideration:
- Material: PLA is a common choice due to its ease of printing and adequate strength for light-duty applications.
- Printer Settings: Settings like layer height and temperature can significantly impact the strength and functionality of the printed bearing.
- Slicing: The design needs to be converted into a format suitable for 3D printing, usually STL, and then sliced using software like Prusa Slicer. It’s crucial to ensure that the design doesn’t require support structures and that the air gaps are correctly set to allow movement.
Practical Applications and Limitations
3D printed bearings are particularly useful for prototyping or applications where the bearing isn’t subject to high loads or critical functions. They are ideal for small toys, DIY projects, or situations where a custom bearing size is needed quickly. However, it’s important to remember that these bearings are not suitable for high-stress applications where traditional metal bearings would be necessary.
FAQs on 3D Printed Bearings
Q: Can 3D printed bearings replace metal bearings in machinery? A: While 3D printed bearings are useful for certain applications, they generally cannot replace metal bearings in high-stress or critical applications due to their lower strength and durability.
Q: What materials are best for 3D printing bearings? A: PLA is commonly used due to its ease of printing and adequate strength for light applications. However, for more robust needs, more advanced materials might be required.
Q: What are the key design considerations for 3D printed bearings? A: Important factors include the size of air gaps, the number of rollers, and the overall dimensions of the bearing to ensure smooth operation.
Q: How do I ensure my 3D printed bearing functions well? A: Proper design, accurate slicing, and optimal printer settings are crucial. Ensuring the air gaps and roller dimensions are appropriate for the intended application is also key.
In conclusion, 3D printed bearings offer a unique and flexible solution for custom and rapid prototyping needs in various applications. While they might not replace traditional bearings in heavy-duty machinery, their ease of customization and production makes them an invaluable tool in the realm of 3D printing and DIY projects.
For more detailed information and step-by-step guides, you can refer to resources such as All3DP, Hackaday, and Instructables.