
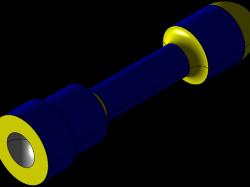
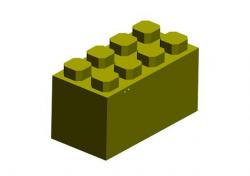

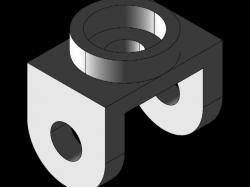
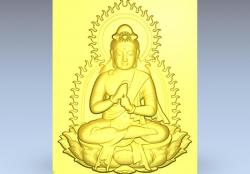
Understanding the BlueMark DB120
The BlueMark DB120 is a compact and lightweight Remote ID module measuring 48 x 38 x 28 mm and weighing just 25 grams. Despite its small size, it packs a powerful punch with a built-in battery and GNSS receiver. It’s designed to be mounted easily on a drone, using 3M dual-lock stickers or M5 screw noses. The module is FAA-approved for use in the USA and conforms to regulations in the EU as well.
3D Printing and the DB120
One interesting aspect of the DB120 is its casing, which appears to be 3D printed from nylon. This raises questions about its durability and lifespan, especially in the demanding environments where drones often operate. The module’s unique L-shaped design, larger than many other RID modules, might pose challenges in mounting and durability. This aspect underscores the importance of material choice and design considerations in 3D printing for drone technology.
Tips for 3D Printing Drone Components
When 3D printing components like the DB120 or similar modules, several factors are crucial:
- Material Selection: Choose materials that are lightweight yet durable. Nylon is a popular choice for its strength and flexibility.
- Design Accuracy: Ensure the design dimensions are accurate to ensure easy mounting and compatibility with the drone.
- Test and Iterate: Always test the printed component for fit and durability, making necessary adjustments for optimization.
Q&A on 3D Printing Drone Components
How do I choose the right material for 3D printing drone components?
Select a material that balances weight and durability. Nylon is often preferred for its strength-to-weight ratio.
Can I customize the design of a component like the DB120?
Yes, 3D printing allows for customization. However, ensure any modifications comply with regulatory standards and do not hinder the component’s functionality.
What are the challenges in 3D printing drone components?
Challenges include ensuring the accuracy of the design, the durability of the material, and the component’s compatibility with the drone.
In summary, the BlueMark DB120 is a notable example of how 3D printing can be utilized in the drone industry, particularly for manufacturing components that must comply with stringent regulations. The intersection of 3D printing technology and drone manufacturing opens up new possibilities for innovation and efficiency in design and production.